Atomoving
Order Picker
Order Picker
Order pickers are essential in various settings where precise item selection and efficient horizontal transportation are crucial. They offer a flexible, effective solution for material handling tasks that demand accuracy in order picking at multiple levels, enhancing productivity and streamlining operations in warehouses and distribution centers.
Enhance warehouse efficiency with our semi-electric order picker, reaching up to 4500mm. Optimized for safety and narrow aisles.
Boost productivity and safety with the warehouse order picker, designed to eliminate ladder use and handle 300kg loads effortlessly.
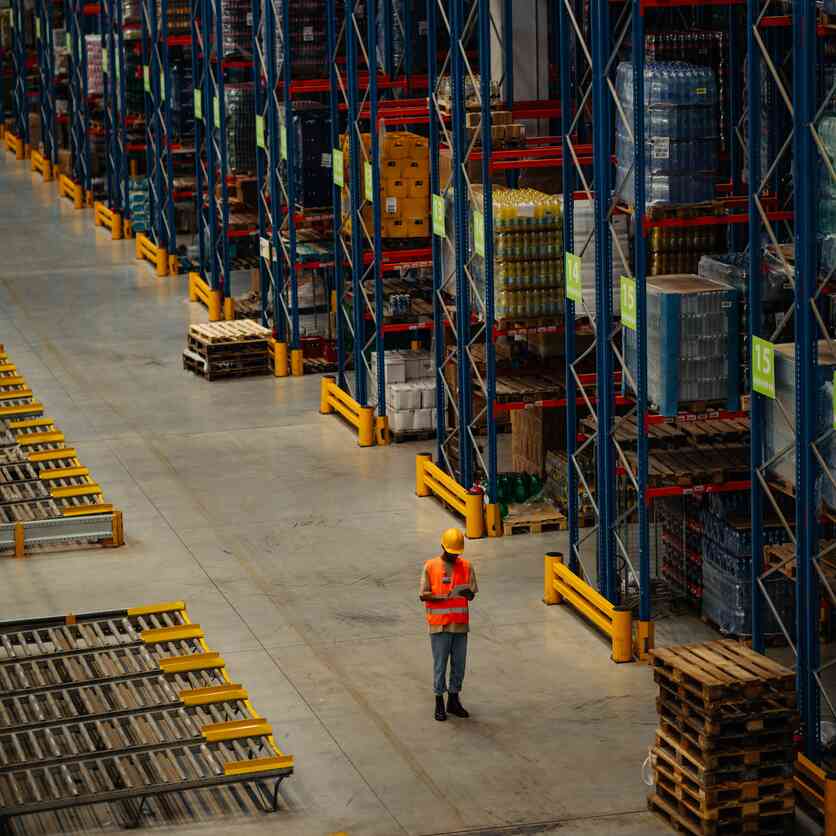
Designed to Perform
The SEP and FSEP Series order pickers are engineered for seamless, quiet operation and effortless maneuverability, ensuring operators experience minimal fatigue and achieve heightened efficiency.
Frequently Asked Questions
What is an order picker?
An order picker plays a dual role in warehouse operations, both as a job position responsible for accurately selecting, shrink wrapping, and preparing items for shipment using identifiers like barcodes, and as specialized material handling equipment that elevates operators to rack levels for efficient item retrieval. This role is crucial for ensuring items are picked, packed securely, and loaded onto delivery trucks, utilizing equipment such as forklifts when necessary. The use of order picker vehicles specifically allows warehouses to maximize vertical storage space and improve the efficiency of picking operations to fulfill customer orders accurately.
Do you need training to use an order picker?
OSHA regulations mandate specialized training for individuals operating order pickers, classifying these machines within the powered industrial truck category. Under the standards outlined in 29 CFR 1910.178(l) for the general industry and 29 CFR 1926.602(d) for construction, comprehensive training and certification are essential. Employers bear the responsibility of ensuring that every operator, whether a direct employee or a temporary worker supplied by staffing agencies, undergoes this critical training regime before handling the equipment unsupervised.
What is the difference between a forklift and an order picker?
The key distinctions between forklifts and order pickers lie in their design, operation, and intended use within warehouse and material handling environments. Understanding these differences is crucial for selecting the appropriate equipment for specific tasks.
Typical Application:
- Forklifts: Primarily used for moving heavy palletized loads, and in loading/unloading and bulk transport tasks.
- Order Pickers: Ideal for selecting less than pallet-load quantities and individual items, catering to piece-picking operations such as e-commerce fulfillment.
Operator Position:
- Forklift: The operator remains inside the cab at ground level, manipulating loads mechanically.
- Order Picker: The operator ascends with the load on an elevated platform to manually pick items.
Lifting Mechanism:
- Forklifts utilize forks to mechanically lift and transport pallets and heavy loads.
- Order Pickers feature a platform that elevates the operator to rack levels for hand-picking individual items or cases.
Power Source:
- Forklifts: Can operate on electric, propane, diesel, or gas power, accommodating a variety of industrial environments.
- Order Pickers: Generally powered by electricity to ensure safe indoor operation.
Licensing Requirements:
- Forklifts: Require an operator to hold a Forklift License (LF classification).
- Order Pickers: Necessitate a separate Order Picking Forklift License (LO classification).
In summary, forklifts are engineered for ground-level operation, focusing on the mechanical handling of heavy, palletized loads. Conversely, order pickers are designed to elevate operators for manual item selection from racks.